
Kounik Maitra
10 January 2023
The Drought of Semiconductors!
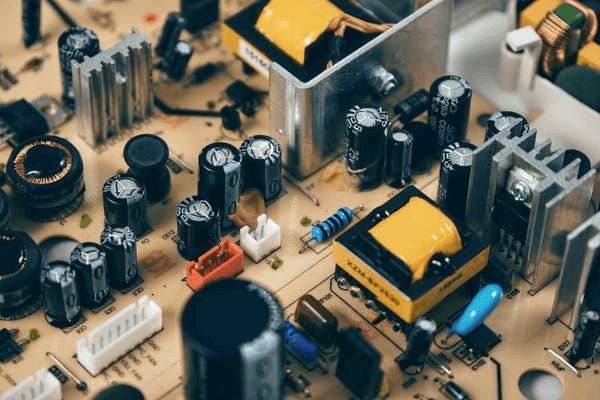

Kounik Maitra
If you are looking forward to buying a graphics card or gaming consoles like the latest PS5 or the brand-new Xbox or a new laptop, you might be out of luck as there is hardly any stock left in the market and whatever is available, is priced pretty high and might not be very budget-friendly to you. Well, the reason is the ongoing Global chip shortage!
Semiconductors, known as "chips," are at the heart of economic growth and an indispensable component of technological innovation. These Nano-sized silicon wafers, thinner than a strand of human hair and consisting of up to 40 billion components, have a gigantic impact on the global economy., because these semiconductor silicon chips are the brains and building blocks of most electronic devices and without these, the smart device won't remain that much "smart" as you expect them to be, yes even the laptop or smartphone on which you are reading the article is no exception.
Let's dive into this global phenomenon and unravel why these chips are so important, how all this started, get a better understanding of the current scenario, and when we can expect the productions to go back to normalcy.
SEMICONDUCTOR CHIPS – WHY THE DEMAND?
Incredibly complex and capitally intense, these integrated circuits (IC) power everything from computers, smartphones, cars, data center servers to gaming consoles. All the modern technological electronics devices that are an integral part of this "scientifically advanced" lives of ours are run by billions and trillions of minuscule electronic switches called transistors. These transistors determine whether the electric signal is high or low, and these highs and lows are interpreted as 1s and 0s by the computing device. Yeah, so that's how these binary signals are fed into your system. These transistors are made on by printed electronic circuits onto semiconductor discs called wafers. Since the advent of microprocessors with the introduction of the Intel 8085 microprocessor, the demand for computer chips has only grown exponentially and so has their designing complexity.
Owing to its designing complexity and minute intricacies the process of chip manufacturing is extremely complicated. Due to this most of the companies such as Intel, TSMC and Samsung run specialized factories called 'fabs' for the process of chip fabrication.
That's not all, if the intricate complexities of chips were not enough there lies an additional hazard owing to the small size of the chips. The chips are so tiny that even a fine speck of dust can tamper the entire wafer, leading to the wastage of potentially hundreds of chips, that's why the fabs are built in some of the cleanest places across the world and follow extremely strict sanitation protocols. The construction and maintenance of fabs is another financial nightmare for companies. Construction and proper equipping of only one fab can cost the company billions of dollars and it takes years to build an industrial fab from scratch.
MAJOR REASONS BEHIND THE CRISIS
THE COVID-19 PANDEMIC
All major companies like AMD, Nvidia, Apple, and Intel run their own fabs or license other fabs to build their designs for them. AMD and Apple generally contract TSMC, while Intel has its own fabs. Whereas Nvidia has opted for a mixture of TSMAC and Samsung for its graphics card.
Typically, these fabs combined hold the prowess of fabricating millions of chips every year, but the impact of Covid 19 derailed the entire production process.
As the countries went into complete lockdown and the work from home came into play, the demand for laptops and PCs went off the charts. This resulted in immense pressure on the fab companies, which conventionally allocate their output to the designated companies, and these companies, in turn, sub-allocate them into their product portfolios.
Let's analyze the pretext under the case for AMD and Nvidia. AMD is a company that makes CPUs and GPUs for PCs, laptops, and a vast variety of semi-custom designs like console chips, and this thins out the number of wafers that they can allocate for each product line. Nvidia also suffers from the same issue but to a slightly less degree since its production lines are meant for CPUs and GPUs for PCs, laptops, and enterprises purpose. All these have put tighter bounds on fab's output production lines and company product stocks. Although all the chips, manufactured are being sold due to the high demand but all the chips are not being directed to the customers.
CHINA-USA WAR AND THE GEOPOLITTICAL TENSION
The geopolitical dimensions of semiconductor-at the heart of the US and China's battle for technological supremacy continue to rise and risk the further splintering of the global supply chains and disordering the international commerce. The geopolitical futurist Abhisur Prakash claims that the chip industry is in limbo he adds that " geopolitics of technology can threaten any sector "
Since the US-China decoupling began to make the headlines in 2017, much of the attention centered on trade and the 5G campaign against Huawei, China's market-leading tech company.
But recent disciplinary actions taken by Washington involving semiconductors pose a much more fundamental problem for Beijing. Efforts to cut off the supply of chips to Huawei and to encourage the construction of advanced semiconductor factories or fabs in the US have dragged the industry into the new tech cold war.
TAIWAN DRAUGHT DRYING UP THE SEMICONDUCTOR MARKET
Taiwan is home to some of the world's largest and most advanced high-tech foundries, a linchpin of a global $450 billion industry that accounts for the computing power for essential devices, but is extremely water-intensive.
In 2021, Taiwan had to experience its worst drought than it has done in more than half a century.
This led to jeopardizes among chip manufactures who need tons of ultra-pure water because Making semiconductors is a hugely water-intensive process throughout the manufacturing protocol, from cleaning the chips themselves to keeping the state-of-the-art foundries hypersterile and washing away waste chemicals. For the record, the TSMC's fabs use more than 63,000 tons of water a day that amounts to more than 10 percent of the supply of two local reservoirs.
THE CURRENT SCENARIO AND SHORTCOMINGS THAT WENT UNNOTICED
The global automotive industry expected that demand for cars would depreciate during the pandemic. After many countries have lifted the lockdowns, the demand for passenger vehicles
(PVs) has considerably increased due to people's general reluctance to travel by public transport.
After the auto industry had restarted production, it faced a shortage of semiconductor chips.
Global carmakers like Ford, Toyota, Nissan, VW, and Fiat Chrysler have scaled back output. The Indian car manufactures have also fallen prey to this global chip shortage.
"The big concern for the auto industry and Mahindra, and in fact for the world, is the semiconductor shortage. It is something that we're very perplexed with, and something where the end is not clearly known as to when this fall will go away," said Pawan Goenka, MD, and CEO of Mahindra & Mahindra, during a press conference while declaring the company's Q3 results, on February 5.
Samsung Electronics Company says that there is a "serious imbalance in supply and demand" for chips. The semiconductor industry is dependent on the foundry model, which consists of semiconductor fabrication plants foundries and integrated circuit design operations - each belonging to separate and distinct companies. The foundry model has resulted in the concentration of the fabrication operations.
As of 2021, only three leading firms can manufacture the most advanced semiconductors - Taiwan Semiconductor Manufacturing Company (TSMC) of Taiwan, Samsung of South Korea, and Intel of the United States. Advances in semiconductor fabrication are determined by the number of transistors, per square millimeter.
The global semiconductor industry is heavily dominated by companies from the Asia-Pacific region including China, Japan, Singapore, South Korea, and Taiwan. The U.S. share of global semiconductor fabrication sums up to only 12%. The increasing reliance by U.S. companies on international partners to fabricate the chips that they design clearly exhibits the United States' diminished fabrication aptitude.
A season of bad weather is also hindering the chip production process in North America. Recently, eight state governors of the U.S. have asked President Biden to redouble efforts "to urge wafer and semiconductor companies to expand production capacity". TSMC recently announced that it plans to invest $100 billion over the next three years to increase capacity at its chipmaking plants, days after which Intel Corporation announced a $20 billion plan to expand its advanced chip manufacturing potential. It may take at least two years for the new dimensions to come into production.
India has also entered the race for semiconductor fabrication supremacy. India is contributing more than $1 billion in cash to each semiconductor company that sets up manufacturing units in the country as it seeks to build on its smartphone assembly industry and extend its electronics supply chain. "The government will give cash incentives of more than $1 billion to each company which will set up chip fabrication units," a senior government official told Reuters a few days back, declining to be named as he was unauthorized to speak with media.
In October, a fire at a Japanese plant belonging to Asahi Kasei Microdevices located in Nobeoka, Miyazaki took away with it advanced sensing devices used in automotive and other industries out of circulation. As of late February, the plant was still down due to damages caused by the fire.
There have also been limitations in the global transportation system. According to Clear Metal, which controls over 90% of ocean freight, nearly 7% of ocean freight is not making it out of China ports this quarter.
The patrol times for chip supplies have stretched up from 10 weeks to about 17 weeks on an average for certain types of microprocessors over the last year, according to data from Bain & Company.
The Texas winter storms forcibly pushed the U.S. power utility, Austin Energy to shut off power to the Austin area's largest electricity users - among them included the chip factories operated by Samsung, NXP Semiconductors, and Infineon Semiconductors.
"The global chip shortage is like a long winter that won't go away so soon," says V Venkateswara Rao, an alumnus of IIM, Ahmedabad, and a retired corporate professional.
QUICK ANALYSIS AND IMMEDIATE MEASURES
Current chip shortages are not confined to critical components and specialized core processors. Shortages are also inclusive of less critical but still crucial components, such as power regulation, which is used across a wide range of end devices. There has been comprehensive coverage of these shortages impacting the automotive industry, but all industries competing with consumer electronics giants for the same components used in both an electric car and your iPhone are bound to feel the impact.
You ask why? Because these seemingly less critical but crucial components are largely manufactured using legacy equipment no longer in production and at fabrication centers whose capacities are already nearly maxed out. As smart devices proliferate, demand for these components will only intensify across all end markets.
Gartner analysts recommend that OEMs dependent directly or indirectly on semiconductors take four key actions immediately to moderate risk and revenue losses during the global chip shortage:
• Extend supply chain visibility – The chip shortage makes it necessary for supply chain leaders to extend the supply chain visibility beyond the supplier to the silicon level, which will be crucial in anticipating supply constraints and bottlenecks and eventually, projecting when the crisis will improve.
• Guarantee supply with companion model and/or pre-investments – OEMs with smaller and critical component requirements must look to partner up with similar companies and approach chip foundries and OSAT professionals as a combined entity to obtain some leverage. Additionally, if scale allows, pre-investing in a commoditized part of the chip supply chain and foundries could guarantee the company a long-term supply.
• Track leading indicators – While no relevant parameter by itself will forecast how the shortage situation will evolve, an aggregate of relevant parameters can help guide industrial organizations in the right direction. "Since the current chip shortage is a dynamic situation, it is essential to understand how it changes on a continuous basis. Tracking leading indicators, such as capital investments, inventory index, and semiconductor industry revenue growth projections as an early indicator of inventory situations, can help organizations stay updated on the issue and see how the overall industry is growing," said Gaurav Gupta, research vice president at Gartner.
• Diversify supplier base – Qualifying a different source of chips or OSAT partner will demand additional work and investment, but it would go a long way in reducing risk.
Additionally, establishing strategic and secure relationships with distributors, resellers and traders can help with collecting the small volume for urgent components.
The global chip shortage is here to say and we may need to face its outrage for a couple of years or more but that doesn't discourage the industry leaders and the hunt for alternatives is on and parallelly the constant effort to kickstart the fabs and the fabrication foundries at their usual intimidating workforce.
"The secondary market for capital equipment is crucial to expanding the capacity of mature nodes. As an industry, they can help add transparency and legitimacy to this supply chain strategy by formally measuring and monitoring the global secondary market for semiconductor manufacturing equipment." -Forbes